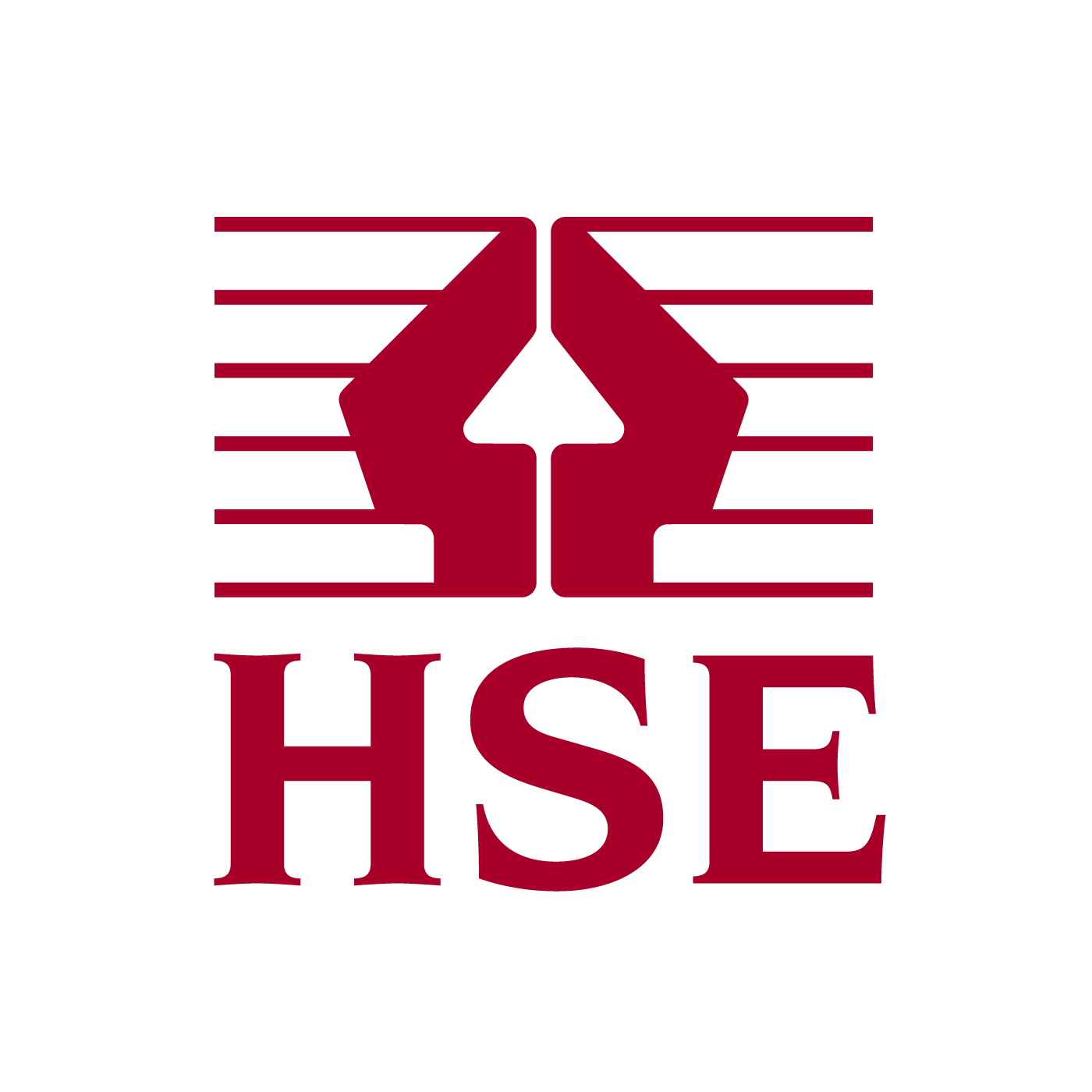
18.2K
Downloads
13
Episodes
In 2022, The Health and Safety (HSE) launched a new 10-year strategy: Protecting People and Places. This is strategy that reflects HSE’s role at its broadest. A role that goes beyond worker protection, to include public safety assurance on a range of issues, as we adapt to new technologies, the government’s commitment to the net zero agenda, and HSE’s added responsibilities, including becoming the appointed Building Safety Regulator, and our extended role in chemical regulation, post Brexit. This Health and Safety Executive (HSE) series of free podcasts will cover a range of subject matters to help businesses and workers understand HSE’s strategic priorities, its campaigns and the main challenges we collectively need to address.
Episodes
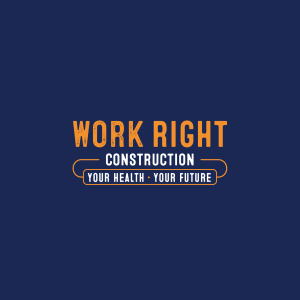
Friday Oct 21, 2022
Manual handling in construction
Friday Oct 21, 2022
Friday Oct 21, 2022
In this podcast, we discuss HSE’s latest construction initiative focusing on the risks of injuries and aches, pain and discomfort in joints, muscles and bones known as musculoskeletal disorders (MSDs).
With 40,000 construction workers reporting that they suffered with MSDs last year, Matt Birtles, Principal Ergonomics and Human Factors Consultant at HSE and Peter Crosland, National Civil Engineering Director at CECA discuss what the industry can do to promote change and protect its workforce.
Amongst other things, the podcast covers HSE’s ‘Your health. Your future’ construction campaign, the impact that these injuries can have on workers and employers legal responsibilities and the sensible control measures that can be introduced regardless of the size of the construction site.
For more information on the campaign visit ‘Your health. Your future'
PODCAST TRANSCRIPT
[00:00:00] Mick Ord (Host): A warm welcome to you whenever you are listening to this Health and Safety Executive podcast from me, Mick Ord, and our soon to be announced guest experts. This podcast will be the first in a series designed to help you to make your life a little easier, both in work and maybe even spilling over into your personal life, you never know.
The health and Safety executive is committed to improving the health and wellbeing of workers in Great Britain. And today we'll be focusing on the construction sector, a key industry that employs more than two million people and includes employers and building workers, contractors and subcontractors, staff and freelancers alike in a range of organisations from sole traders to multinationals.
Last year did the UK alone, 40,000 construction workers suffered from injuries and aches, pain and discomfort in joints, muscles and bones. Such injuries can have a serious impact on their ability to perform tasks, their quality of life, and in some cases their ability to stay in work and earn a living or having to take time off work as well.
Many people suffer from long term pain and discomfort as a result of injuries sustained on building sites. So with such worrying stats in mind, the HSE are embarking on the Work Right construction campaign. This means that HSE inspectors will be performing a thousand inspections at building sites in the UK.
So what will they be expecting from companies? Joining us is Matt Birtles, an ergonomics expert from the HSE Science Division, and a little later we'll be hearing from Peter Crosland, the National Civil Engineering Director at Ceca, the Civil Engineering Contractors Association.
Well, first of all, Matt, thanks for joining us for the podcast. What should companies expect if an inspector does visit their site?
[00:02:18] Matt Birtles: First and foremost, thank you Mick for hosting us and having us on this podcast. When
an inspector comes knocking on site, first and foremost, expect the norm. So they'll be looking at safety as well as health issues. But what's happening during the campaign especially is there'll be an increased focus on particularly the kinds of risk factors associated with musculoskeletal disorders.
So there's been an awful lot of effort ahead of this campaign within, you know, my regulatory colleagues in HSE to train them upon understanding the key risk factors. For musculoskeletal disorders, how to assess them and what kind of controls they might want to see in place. And so when the inspector does come, they'll be looking at the kinds of manual handling activities and maybe some repetitive work that commonly go on in construction sites and looking specifically at ways in which the risks are controlled.
So there may be some of that manual handling activity happening during the inspection, and they'll just observe that and watch how it's done, where potentially improvements could be made. And also looking at the paperwork and the risk management system. If there aren't any manual handling operations happening at the time of the inspection, they're just more likely to ask principal contractors or ask them on site responsible for safety about manual handling, and ask them to show them their risk management systems, any risk assessments they have, any planned risk controls.
Especially at those points where you'd expect increased manual handling. So moving materials around during deliveries, for example, during fitting or moving plant equipment. And so just an increased focus on musculoskeletal disorders in every inspection for the next six weeks or so.
[00:03:57] Mick Ord (Host): And who specifically is the "Your Health, Your Future" campaign aimed at?
[00:04:02] Matt Birtles: The target really is anybody involved in construction. And so while obviously anybody on the site, you're more likely to see colleague inspectors or regulatory colleagues, we'll be looking at those involved in the design and then planning of construction, and procurement, for example, and then certainly those on the managing sites and working on sites and doing the physical tasks on sites.
And it's aimed at larger construction sites or smaller. And so we're going to try and focus on as many sites as we possibly can and as greater variance as possible. But everybody has responsibility for helping to manage MSDS or musculoskeletal disorders.
[00:04:43] Mick Ord (Host): And why the focus now on the manual handling assessment?
[00:04:48] Matt Birtles: Well, manual handling assessment. It's gotten easier over the years with the advent of the HSE tools like the MAC tool or manual handling assessment charts or the RAPP tool risk assessment for pushing and pulling. For, you know, barrows and the like, Manual handling assessment has gotten much easier. And while doing the assessment using the tile method or L23 method, it meant all the methods involved a checklist of looking at all the different risk factors.
It could be quite arduous and not necessarily give you the answers that would lead neatly to potential solutions. Now, with the MAC tool, which is not new, there's nothing new in the MAC tool per se. It's much easier to actually do a quick assessment and wherever identifying manual handling operations. It's very quick and easy now – even using the online version, which is the new element of all this I suppose – to do a quick assessment and understand the key risks and level of risk. And so the barriers have gone for potentially, arguably, long and arduous risk assessments. It's now very straightforward to do a risk assessment, and so it shouldn't be a barrier anymore.
[00:05:54] Mick Ord (Host): And how serious is the problem of injuries sustained in moving and handling construction materials?
[00:05:59] Matt Birtles: Inevitably being who I am, where I'm from, I'm going to say very. But actually the stats do add up. As you mentioned, 40,000 injuries per year on average in the construction sector. But if you compare that to other industries or the rest of all industry, you’ve kind of almost got double the rates of musculoskeletal disorder amongst construction workers.
So, while across industry, we might see roughly speaking about 1/100 workers getting injured with musculoskeletal disorder, in construction, it's around 1/50. So about 54% of ill health for the construction sector is musculoskeletal disorders. So it's far too common. It affects far too many lives.
Then the other way of looking at how serious it is, is what's the impact on individuals and per individual? What happens to that person, and we may cover this a bit later, but it can affect every aspect of life. Of course, as you mentioned it can impact on your ability to actually go to work and earn a living. But also it can impact on your home activity, mucking around with your kids, the enjoyment you might get from normal stuff like going down the pub, going to the cinema, and those sorts of things.
Because of the nature of the discomfort with MSDs, it can actually affect your ability to stand and make that uncomfortable, but also your ability to sit down and make that uncomfortable. So in those sorts of areas, it becomes very serious because it can really deeply impact on people's health and wellbeing, not just in work, but also outside of work.
[00:07:28] Mick Ord (Host): Peter Crosland from Ceca, Peter, have you got some examples of the kind of injuries that workers have sustained and the actual impact it's had on their lives?
[00:07:38] Peter Crosland: Well, yes. Thanks Mick. And I think yes, all too often where you get examples of people who have worked in the industry for a long time and then suddenly become unable to work.
And coincidentally, I was at a meeting this morning up in the northeast where one of the previous site supervisors had worked for 20 years laying curbs. And actually had a back that was quite wrecked and he really was in a quite a difficult place. And I think we just hear that story all too often. So one of the problems has been the latency effect of all these issues coming to the surface, and I have to say that given the nature of our workforce, which is, I think we'll all know that demographics by now, they've been banded around. You know, many times that there are a cohort of people who have carried out those activities and are now suffering really quite badly, and they're having to move jobs. They're having to step down away from the work that they really, you know, they joined the industry to do and they can no longer carry out those functions. And as Matt says, that then starts to spill over into home life and it affects the quality of life of not only the worker, but also the family.
[00:08:57] Mick Ord (Host): And in that particular example that you just quoted from the northeast, is there anything that you can do to help that particular person if they've been manual handling in a certain way for 20 or so years?
[00:09:10] Peter Crosland: This is probably going to sound slightly negative, but I think sometimes we are a little bit reactive in the industry rather than proactive. Unfortunately, you have a whole host of workers who have operated in a slightly cavalier manner. Perhaps they didn't know better. And then as we have known, and certainly Matt's team have discovered through the statistics, that actually this is what's happening to the workforce and therefore we need to go and find ways of making sure that that doesn't happen again.
And I think you can cite examples right and way throughout all the activities that certainly we were involved in, whereby, you know, we're always looking to see how we can improve matters for every worker.
[00:09:55] Mick Ord (Host): Matt, with regard to the HSE visits, will companies being given prior notice or will they just turn up?
[00:10:02] Matt Birtles: Generally we'll just turn up, There's not a specific requirement to give a prior notice.
It may well be that a site's already got a planned inspection or a meeting with a regulatory colleague, and that will then turn into a musculoskeletal disorders focused inspection. But unless you've got already something planned in the next six weeks with a regulatory colleague, no, expect them to just turn up an announced.
[00:10:26] Mick Ord (Host): How are the construction sites chosen beforehand?
[00:10:30] Matt Birtles: Well, no sites are exempt, so any site could be visited by a regulatory colleague. Inspectors generally visit sites that are known to be higher risk, and there is some intel on that. There's a number of ways to identifying the sites to visit. The F10 notification database that we have on sites where we've had an instance before, perhaps sites where some concerns have already been brought to our attention through various means or sites, perhaps where they've received RIDDOR accident forms, or they've had RIDDOR reportable accidents in the past that have not previously been selected for investigation.
There'll be some channelling with that along with a sort of local intelligence as well. Knowing where the sites are, but the sites, there's no specific requirement or desire to pick just on small or just on larger sites. Any site could be visited to be perfectly honest.
[00:11:18] Mick Ord (Host): And what does the law say about what employees need to do to protect their workforce?
[00:11:23] Matt Birtles: There are various laws. I suppose the one that's most specific to this campaign is the manual handling operations regulations. It's relatively straightforward, to be honest. In fact, if you ask any of my inspector colleagues – where I'm from in in the agency, it's our privilege to often train them – I imagine most inspector colleagues will say one of three words, and that's AVOID. ASSESS. REDUCE.
So the law pertaining to manual handling is avoid hazardous operations. Now, that's important. It doesn't say avoid manual handling anywhere in the law. in fact, good manual handling is actually good for you. It does keep you fit, keep your muscular, and potentially there’s research that suggests you may live longer. So don't avoid all manual handling, but avoid hazardous operations wherever you possibly can.
But if you can't avoid hazardous manual handling, then we don't immediately, you know. Put in a claim or something. We assess those hazards. We assess the risk using usually the MAC tool and the RAPP tool initially, and that's a five-minute task. It'll take longer to, you know, find it on the website maybe than actually to do an assessment.
But I promise you the second assessment, you deal with will take five minutes, and then you assess those tasks to understand the risk in order to reduce the risk. This is where the rubber really hits the road, in terms of risk management. We can have lots of really nice – in terms of the MAC and the RAPP tool – very colourful assessments. But unless they're used to actually challenge the tasks and make those tasks easier to do risk reduction by making the jobs easier, then it's just from the paperwork.
So avoid, assess, and reduce risk is what it's all about.
[00:12:59] Mick Ord (Host): And Peter, what are the barriers to employers and workers on sites?
[00:13:04] Peter Crosland: I, I think there are many barriers, but I think it depends what type of site that you are looking at. What we find within Ceca particularly, we have a very broad church of members. So ranging from tier ones through to SMEs, almost on to solo practitioners in some cases, although they're not direct members because we do have limits on that.
But I think one of the barriers will be for those, I would say, down the supply chain to be able to access the information and training that they need to carry out the work properly. So, you know, we've already mentioned the fact that yes, there is a legal requirement and there are others that apply as well.
Obviously, you know, not least the ‘74 Health and Safety at Work Act, you know, we have as employers, have a duty of care. So regardless of where those people are in the supply chain, there is somebody responsible for that person. I actually, a bit like Matt, I split the sort of desires into three parts really.
There is a sort of like a MUST DO, a SHOULD DO, and a COULD DO.. And that's where the barriers are really, because most do apply the MUST because it is a legal requirement, obviously. There is the SHOULD, which perhaps includes specific training around those lifting requirements that might generate those MSDs. But actually then there's the COULD. You know, what could clients and organisations do to really help the workers make sure that they don't suffer or are made ill through their work? So things like that would be really trying to engage with them, almost a one-to-one, job specific level, to say “Well, look, this is what we've got to do. How do you think we are going to do it?” And I don't think that happens often enough.
[00:14:49] Mick Ord (Host): And Matt, what do employers need to know and do now prior to the possible visit?
[00:14:56] Matt Birtles: Look at their risk management systems they've got in place. That may be occasionally dusting those off or just making sure that they're up to date.
And so that means, you know, looking at the paperwork they've got in terms of a local policy, a local approach to managing musculoskeletal disorders, having a look at the risk assessments that they've already done, and do they still match the tasks? One of the things obviously about construction is they have a changing environment.
So do they need updating and do you need to re-challenge some of the work that's done?? It may have changed since the last assessment, and again, I absolutely agree with what Peter just said through engagement with the workers. So obviously the colleagues who are actually doing the work know what's changing in the environment better than any of us.
Have a chat with them to make sure that the risk assessments are covering the right tasks in terms of, you know, risk profile or effectively, are they the hardest tasks that the people on the sites would prefer to avoid? If they can, are they looking at the right tasks? And if not, maybe add to the risk assessments.
Make sure that you're assessing those tasks that are identified through engagement are the ones that potentially have the greatest level of risk. And then look again at the solutions they've got in place. You know, download those hire catalogues and have a look at what's available and perhaps challenge what is being done.
Is there anything that can be done on the sites that would avoid or eliminate some of the heavier activity by putting things on wheels or using mechanical aids? Just sharpen things up. I'm sure you know, the majority of sites have got risk management in place. Just make sure that that's ready because they're the sort of things that the inspector colleagues will be asking for when they do come around.
[00:16:38] Mick Ord (Host): And Peter, you've already mentioned that the guidance is relevant to small builders as well as large builders. What about subcontractors?
[00:16:46] Peter Crosland: Well, that's even a more difficult to nut to crack, I think. And it's really trying to get that message right throughout the supply chain. So I don't think there's any easy answer to this.
We certainly, within Ceca and also working with HSE, it's very difficult to try and get a common message out to all of the industry, and almost by saying that each part of the industry also almost needs a specific message as well. So we do really work quite hard at trying to get the right message to the right people at the right time.
And obviously small builders, small organisations are part of that conundrum, if you like. So certainly not an easy answer there, Mick. And I think we're all searching for that holy grail in being able to, as I say, do exactly that – get the right message to the right people at the right time.
[00:17:37] Matt Birtles: I concur. That is the challenge, isn't it? Getting the message to the smaller enterprises and the refurb kind of sites is a challenge. While largely the messages are the same for those sites, proportionality and practicability may mean that the kinds of solutions we would expect to see or hope to see under smaller sites would be far less than those on the larger. There’s just not enough money washing around to go to the higher companies and get the largest solutions. And so, we have to be quite pragmatic about what we should expect. But the guidance is still relevant. It's just proportionately, we may expect a little bit less in terms of expenditure on, you know, the various solutions that are out there for smaller sites.
[00:18:18] Mick Ord (Host): If a company doesn't satisfy the criteria laid out by the inspector, then what are the penalties, Matt?
[00:18:23] Matt Birtles: Obviously it depends, and it's still always going to be proportionate to the level of risk. And so, we'd look at the circumstances at each campaign inspection individually. We'll be looking at the relevant standards, the relevant working practices, you know, see how far we are from good practices. For example, using HSE's enforcement management model, which standardises enforcement activity across any sector, anywhere, and looking at the enforcement policy. It could be that, you know, generally speaking for lower-level breaches, verbal advice or perhaps maybe a notice of contravention letter will be used in some circumstances where the gap from good practice or the levels of risk that aren't managed are a bit higher. It could be an improvement notice, and yes, it could be a prohibition notice where there's a more significant risk involved.
So we would expect it to be, you know, across the range of potential enforcements, but as far as I'm aware, there's not a target to, you know, suddenly increase the number of prohibition notices or something to be guided by the risk assessments.
[00:19:25] Mick Ord (Host): And will the inspectors be speaking to individual workers on site?
[00:19:29] Matt Birtles: Yes. I mean, not to try and catch them out or anything. Not to try and point any fingers or blame at any individual. But a part of risk management is making sure that individuals understand the kinds of risks they're exposed to. And have been, you know, informed about levels of risk of certain tasks, have been informed on how to use safe operation procedures, and that could be how to use plant equipment or mechanical aids, for example. And also being informed about the end of any risk management processes. Once we've fixed everything we can through mechanical means and engineering risk out, we'll always have some residual risk at the end that we mop up with training.
And so just to find out how well the trainings worked, the manual handing training, for example: has it landed? Has it been successful? Has it changed behaviour? We'd find that out from talking to individuals on site, not trying to pick upon the individual or point a finger and blame anybody, but just to get the general picture of how risk is managed on that side. There certainly could be, yeah.
[00:20:30] Mick Ord (Host): And is there anything in particular that individual workers will be expected to know?
[00:20:37] Matt Birtles: Yes. I think in terms of risk communication, the kinds of risk factors that they're exposed on site, or the key risk, the higher risk activities, what they may be and how they should accommodate them through RAMS or through safe operating procedures. We would expect anybody on site to know who they need to speak to, if they see any issues that concern for near miss reporting, or for, you know, just reporting potentially hazardous activity, which can happen. We all humans make errors, and we always see something a bit wrong. Where would we go to report that and what would the expectations be on any site?
And then yeah, absolutely. The general health and safety training in manual handling training, for example. God forbid they are quoting HSE sentences that we use. We've taken a lot of the words that are given in manual handling training and made them far less fun. So we certainly wouldn't be an examination – "can you quote our particular guidance?" But the general kind of approach to practices. You know, when was the last time that they were sort of reminded of those approaches and did it land? Those are the kind of things we do want people to know about so that they are empowered, as Peter mentioned, for that level of engagement's important. And that's kind of what we're looking at there to make sure that that side of engagement's happening successfully.
[00:21:57] Mick Ord (Host): And how will you know if the campaign has been a success? How will you measure its success?
[00:22:03] Matt Birtles: Well, this is the first year of a multi-year campaign targeting ill health in construction. So we'll measure the impact of this campaign using the information gathered by inspectors while they're on site. Things like material breach rates or the number of inspections that leads to finding material breaches will be one metric. And then others regarding awareness and behaviour change, as best we can, based on observation. How many sites do we leave having made an immediate impact or a subsequent impact in terms of behaviour changes? But because this is the first campaign in the sector targeting MSDs in quite a while, one of the core objectives of this whole campaign is to provide a detailed knowledge of the state of play across the sector to allow HSE to adapt its approach in subsequent years on how best to support employers and protect workers in the construction industry. So, A lot of the work is going to be about what was effective and that's going to really channel our efforts in future years as we run the next year of the campaign.
[00:23:06] Mick Ord (Host): And I guess that's something that you would echo as well, Peter Crosland?
[00:23:10] Peter Crosland: Absolutely. We can't solve the issue of MSDs in in one fell swoop. As Matt says, it's an ongoing process. MSD issues have taken a long time to surface. Hopefully it won't take us long to resolve, but as we become more aware of the issues and also I think particularly, not to miss out on the fact that we're becoming aware of workers' presenteeism. So even if they are actually suffering with an MSD, because of the financial crisis that we're running through and have been running through for a while, you know, people feel compelled to go to work. So they're forcing themselves to work when they're not actually maybe running at 90%. So we need to keep on top of MSDs and certainly as Matt outlined right at the start, we did some work about five years ago to try and identify the financial cost of MSDs In terms of ill health to the industry. And we worked out, it was round about the 75% mark. So, you know, when you then compare it to the likes of occupational asthma, silicosis, asbestosis, occupational dermatitis, noise induced hearing loss, etcetera, MSDs are simply huge. So it really is. And I'm pleased to hear what Matt said, that it is part of an ongoing campaign that will be repeated on a regular basis.
[00:24:31] Mick Ord (Host): Well look, gentlemen, thanks your lot for that. Anyone listening needs to go onto the HSE site, don't they, if they want a little bit more information about the tools that are available for them and all the stuff you've spoken about. So Peter Crosland from Ceca and Matt Birtles from the HSE Science Division, many, many thanks for joining us on the HSE podcast.
[00:24:53] Matt Birtles: Thanks very much indeed.
[00:24:55] Peter Crosland: Yeah, thank you Mick.
14 days ago
Great
14 days ago
Great and thank you